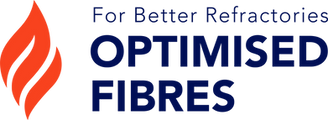
HCA Steel Fibres for Refractories Engineering Advantages
The Chrome content of our HCA steel fibres provides excellent resistance to oxidation but it is the content of Aluminium which enables the fibres to operate so successfully in demanding applications. The Aluminium is homogenously-dispersed throughout the steel and at temperatures around 600ºC begins to migrate to the surface of the fibres where it forms a dense coating of alumina (Al2O3). This protective layer of alumina bonds tightly to the fibre thereby effectively shielding it from oxidation as well as from various forms of chemical attack in aggressive atmospheres.
​
We strongly believe that our drawn-wire HCA steel fibres have engineering advantages when compared to other grades of fibres commonly used in other alloys such as 446, 304, 310 and 330, especially those manufactured by the melt-extraction method. Here is why:
01
Resistance to oxidation
The HC-A alloy is designed to deliver exceptional resistance to oxidation and the fibres can be used at significantly higher temperature ceilings.
03
Higher "hot strength"
Nickel alloys are used to provide “hot strength” but in practise these austenitic grades have only a fraction of the tensile strength of HC-A fibres. The tensile strength of both 304 (1.4301) and 310 (1.4845) will fall to around 50MPa at 1000ºC, at which temperature HC-A fibres with 750MPa will be fifteen times stronger. Melt-extracted fibres in general have relatively poor tensile strength and will break, even at room temperature.
The high load-carrying capacity of the HC-A fibres at elevated temperatures means that refractories are better supported to withstand mechanical shock and abrasion.
05
Homogenous dispersion
Melt-extracted fibres are prone to produce ‘birds’ nests’ in the refractory mix. These can produce hot-spots and corresponding areas with low levels of fibres, which will threaten the integrity of the refractory and cause premature wear.
The easy-flowing characteristics of the HC-A fibres promote a homogenous dispersion of the fibres within the matrix. This is of fundamental importance to correct refractory reinforcement.
07
High level of inter-batch consistency
Compositional and dimensional batch and inter-batch variance is not uncommon in melt-extracted fibres which make full use of the ASTM’s generous tolerances (+/- 10% â„“ and Ø). It is accepted as normal to find very thin or very short fibres packed into the same carton together with very fat or very long fibres.
HC-A fibres have a very high level of consistency, both compositional and dimensional.
02
Successfully operate in cycling temperature regimes
Austenitic (nickel-bearing) fibres such as 304, 310 and 330 are not recommended for applications with cycling temperatures because they have a relatively high coefficient of thermal expansion. Constant expansion and contraction cause spalling of the protective oxide formed on the fibre which in turn provokes spalling of the surrounding refractory.
04
Not susceptible to sigma phase formation
After long-term exposure within the temperature band 590 - 870ºC, some alloys – and in particular 310 (1.4845) – are susceptible to embrittlement by sigma phase. This is the precipitation of a brittle compound within the microstructure of the steel which can cause the steel to become very brittle and bring about catastrophic failure.
06
Not susceptible to sulphidation
In sulphurous atmospheres, austenitic alloys are susceptible to attack resulting in the formation of eutectic nickel sulphides (Ni3S2) with a melting point around 645ºC. Even at such modest temperatures considerable damage will be done when these melt out leaving the fibres exposed to further corrosion and eventual destruction leading to refractory failure. Austenitic alloys are therefore unsuitable for many applications in the steel, cement and petrochemical industries where there are circulating sulphurous gases.
In contrast, HC-A fibres are not susceptible to sulphidation and are well-suited for these applications.
08
A clean finish
Detached oxide swarf is often found in the packaging of melt-extracted fibres in particular. This will normally find its way into the refractory mix where it is nothing more than a contaminant.
HC-A fibres have a bright, clean finish with no swarf.